Processing Ceramic Matrix Composites via Chemical Vapour Infiltration: a CEM-WAVE-based overview
We invite you to delve into the meanders of the Chemical Vapour Infiltration process! Welcome on a captivating journey hosted by one of our subject-matter experts.
By Laura Aliotta (Università di Pisa, UNIPI)
Cost is a proven barrier to the broadening use of Ceramic Matrix Composites (CMCs) over the past decade. Mainly, two factors influence the price of these materials: the high cost of ceramic fibres and the complexity of manufacturing the matrix. As observed for carbon fibres, the necessary conditions to significantly reduce the figure for ceramic fibre are the increase in market demand and the subsequent stimulation of mass production.
As per the possible matrix manufacturing routes, they usually imply expensive batch processes operating at high temperatures and in a controlled atmosphere, leading to a figure that, for a final CMC component, can range from some hundreds to nearing the thousands of €/kg. Therefore, CMCs are expensive compared to other materials, and their high price must pay off by offering a longer service life and unique performance in value-added products.
Specifically, long fibre reinforced CMCs are commonly fabricated through infiltration methods, in which the ceramic matrix is formed from a fluid infiltrating into the fibre’s structure. These techniques differ in the types of fluids and the processes used to convert such fluids into ceramic.
Among them, we find the Chemical Vapor Infiltration (CVI). In CVI, a ceramic gaseous precursor infiltrates a porous preform and is thermally decomposed to a ceramic material through chemical reactions on the fibre surfaces, thus filling the pore network and densifying the composite. The advantages of the CVI are several. For example, the possibility to manufacture complex near-net-shape components at relatively low temperatures and pressures. Or the deposition of a stoichiometric matrix with fine control of the related microstructure, leading to robust, strong composites with good erosion, corrosion and wear resistance properties. Despite those advantages, the main drawbacks are the long manufacturing times of the order of several weeks and the run-to-run reproducibility, which severely limits the usage of this technology.
Commonly, CVI processes differ depending on the heating method (inductive, radiative, plasma or microwave-assisted) and the presence/absence of temperature or pressure gradients inside the reactor. All of those methods are at different levels of technological and industrial maturity. Usually, data on particular processes are also unpublished or unavailable.
Thanks to its capacity to simultaneously infiltrate several complex-shaped preforms, the isothermal-isobaric variant (I-CVI) was the first industrially well-established CVI process. In this process, the preform is placed inside an isothermal-isobaric reactor and filled with the gaseous precursors. The latter flows outside the preform by convection and inside by diffusion. The procedure requires choosing operating parameter values that avoid the premature occlusion of surface pores, which generally leads to temperatures around 1000 °𝐶 and pressures below 100 𝑚𝑏𝑎𝑟, resulting in an uneconomically slow process with reduced deposition yield rates. Moreover, sample thickness is limited to ̴5 𝑚𝑚. If not, two or more infiltration steps would be required to densify higher thicknesses preforms.
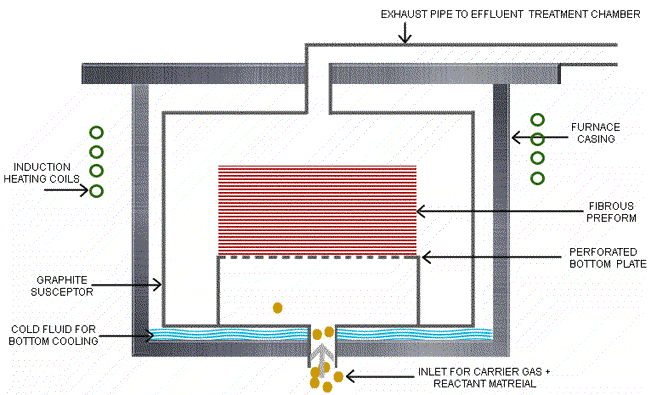
The other variants of the CVI process were born with the idea of overcoming the drawbacks discussed above by the application of pressure or thermal gradients through the wall’s thickness (alone or in combination) to avoid the fast matrix deposition on the external surface.
In the thermal gradient CVI process (TG-CVI), the matrix deposition moves from the hotter outlet side to the colder inlet side due to the increased thermal conductivity of the infiltrated preform. Here the deposition front follows the thermal one, allowing the infiltration to progress uniformly from the hot side to the cold side. Similarly, in the forced flow CVI process (F-CVI), a pressure gradient pushes the precursor reagents within the porous network, thus improving the gas diffusion into low permeability frameworks. It is possible to operate the F-CVI both in isothermal or thermal-gradient conditions.
Another variant of the CVI process is the pulsed flow CVI process (P-CVI). This process is based on a cyclical injection feed of fresh reactants when removing the reaction products, allowing to easily control the residence time of the reactants inside the preform. Moreover, this method allows for the deposition of multi-layered ceramic deposits, changing the precursors along the process. However, since it requires large furnaces and the pumping of vast amounts of gases, the procedure showed technical liabilities for industrial transfer.
The temperature difference is a crucial controlling parameter since it allows tailoring results in the desired deposition profile inside the preform. However, the control of the densification front is not trivial and could lead to undesired density gradients. It is also fundamental to balance the total flow rate to achieve a uniform deposition of the matrix. The pressure difference necessary to achieve the required forced flow inside the preform depends on the pore geometry and spectrum. At the same time, each of these solutions demands complex devices for temperature and flow control, which further increase the capital equipment cost and make scaling-up even more problematic.
Especially concerning new manufacturing technologies, great efforts are at play to develop smoother, more viable and efficient approaches. Even if they exhibit reduced flexibility compared to conventional industrial technologies, such approaches could provide relevant advantages for specific matrix compositions and/or application fields and develop innovative methodologies for technology scale-up.
In the CEM-WAVE project, we address the above-cited drawbacks using the microwave-assisted CVI (MW-CVI) process. The latter exploits benefits such as the inverse temperature profile and the fast and selective heating mechanism to achieve a clean and efficient solution for the sustainable production of silicon carbide-based (SiC-based) CMCs. Nevertheless, using microwave heating generally leads to additional problems and challenges for the effective processing of materials. During the infiltration process, the formation of hot spots in the sample and the appearance of plasma regions at relatively low operating pressures can be particularly detrimental because they damage the sample surface and substantially alter the electromagnetic response of the reactor.
The usage of the MW-CVI process for SiC-based CMCs production displays several and still unexplored possibilities, which we will address throughout the project. We will start by replacing the more cost-effective but much less manageable magnetrons with fully controllable solid-state sources. This quality enhancement will further improve the capabilities of the MW-assisted process in terms of operating conditions, reliability and automation.
Follow our blog in the coming months to know more!