What if the future of steel processing involved microwave technology?
Microwaves and metals, seriously? Despite sounding like a contradiction in terms, microwave technology and steel processing can go hand in hand towards reduced costs and a healthier planet.
That time you burned your microwave oven, because of forgetting a steel fork in the bowl you were warming up your left-over pasta in, might make you think that metals and microwaves are highly (and dangerously) incompatible. However, your worried mother might be amazed by the range of possibilities now available for microwave use in metal processing.
Steel is the most commonly used metal in the world. According to ArcelorMittal’s Climate Action Report 2018, the global demand for steel has more than doubled since the nineties, due to its wide use in equipment, buildings and infrastructure. Although steel production emits lower CO2 per application compared to other materials, the steel industry still contributes to the emission of over three gigatons of CO2 worldwide per year.
Under current consumption patterns, the world’s demand for steel is forecasted to grow from the 1.7 billion tons recorded in 2018 to 2.6 billion tons by 2050. If the industry wants to continue developing, without interfering with the objectives fixed by the Paris Agreement and the European Union (EU) Green Deal of zeroing CO2 net emissions by the same forecasted year, it must shift to cleaner production technologies. One of these being, indeed, microwave processing.
Microwave technology has demonstrated to be a versatile and powerful tool for material processing. It might even become the most popular choice in the near future. Since microwaves deliver electromagnetic energy directly at molecular level, where radiations are absorbed, targeted materials heat up quickly, faster and more efficiently, reducing processing time, costs and even carbon emissions.
Technical studies applying microwave technology to steel production have been ongoing, especially in the United States, for over fifteen years now, arguing such method could cut production costs up to 50%. However, the practical uptake from the sector appears to have been limited. Within the last couple of years, though, it seems to have picked up again, with new papers being published and new projects, such as CEM-WAVE, receiving the necessary financing.
The CEM-WAVE project, in particular, explores how the lifetime of radiant tubes used in steelmaking furnaces and their maintenance cost is key to the efficient application of microwave technology in heat treatment. While, currently, steelmaking production employs metallic alloys within its furnaces, the CEM-WAVE project wants to substitute them with Ceramic Matrix Composite (CMCs) materials, which display superior thermo-mechanical properties, improved efficiency and longevity.
Among the available manufacturing methods of CMCs, Chemical Vapour Infiltration (CVI) has been identified as very effective. CVI is an engineering process by which a material, in our case ceramic, is infiltrated in vapour state into a preform, a ceramic compound compressed into a given shape, often cylindrical. Such preform is of fibrous nature and is heated at relatively high temperature. When infiltrated, the gas fills the spaces between the fibres and reacts with the heated material of the preform, depositing into layers. Once cooled down, the resulting CMC is stronger and more resistant to thermal shocks, when compared to the preform’s material.
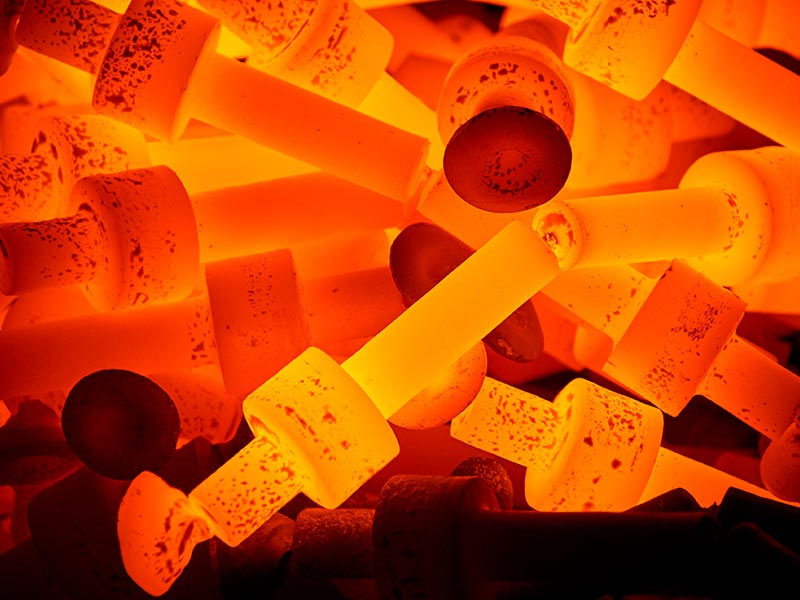
CMCs are known to be very expensive, partly due to the high costs of the raw resources and partly due a very pricey processing technology. Using microwave to assist CVI processing is a way to reduce these costs and make CMCs more accessible not only to steelmaking, but also to other industries.
In fact, using microwaves to produce CMCs seems to have many advantages. Among these, microwaves help in heating the centre of the material faster than its surface. Leaving the surface at cooler temperature lowers the risk of damaging the internal fibres, cutting errors to the minimum. In addition, various academic studies and previous EU-financed projects, such as the HELM project, showed that using microwaves to enhance the CVI process can reduce fabrication times from several hundred hours to around 100 hours, end even less when combined with other technologies.
An industry that employees over 6 million people, it is imperative for steelmaking to evolve in equilibrium with the planet and humanity’s needs. Not as much as your usual kitchen oven – but, who knows? – radical innovation in steelmaking radiant furnaces is awaiting for temperature and corrosion-resistant materials to be implemented at accessible costs. Thanks to projects like CEM-WAVE, this might become possible sooner than we think. The future seems not that far, after all.
Curious about learning more? Watch the CEM-WAVE project video.